Vertical system coatings
System coatings
Optimum protection achieved with high-quality and durable coatings
In the case of vertical system coatings, different coatings are combined to create a multi-layer coating structure. This results in a high-quality and durable coating that offers optimum protection.
Vertical system coatings from FreiLacke have various uses, such as the coating of switch boxes or radiators, as well as within the automotive industry, shipbuilding or corrosion protection. When refining visible areas or decorative features, a major emphasis is placed on an outstanding appearance – in particular within the automotive industry. A good example of an application method is coating light-alloy wheels with a primer, basecoat and top coat (clear coating). The more valuable the final product, the more important it is that the individual coating components interact and are of a reliably high quality.
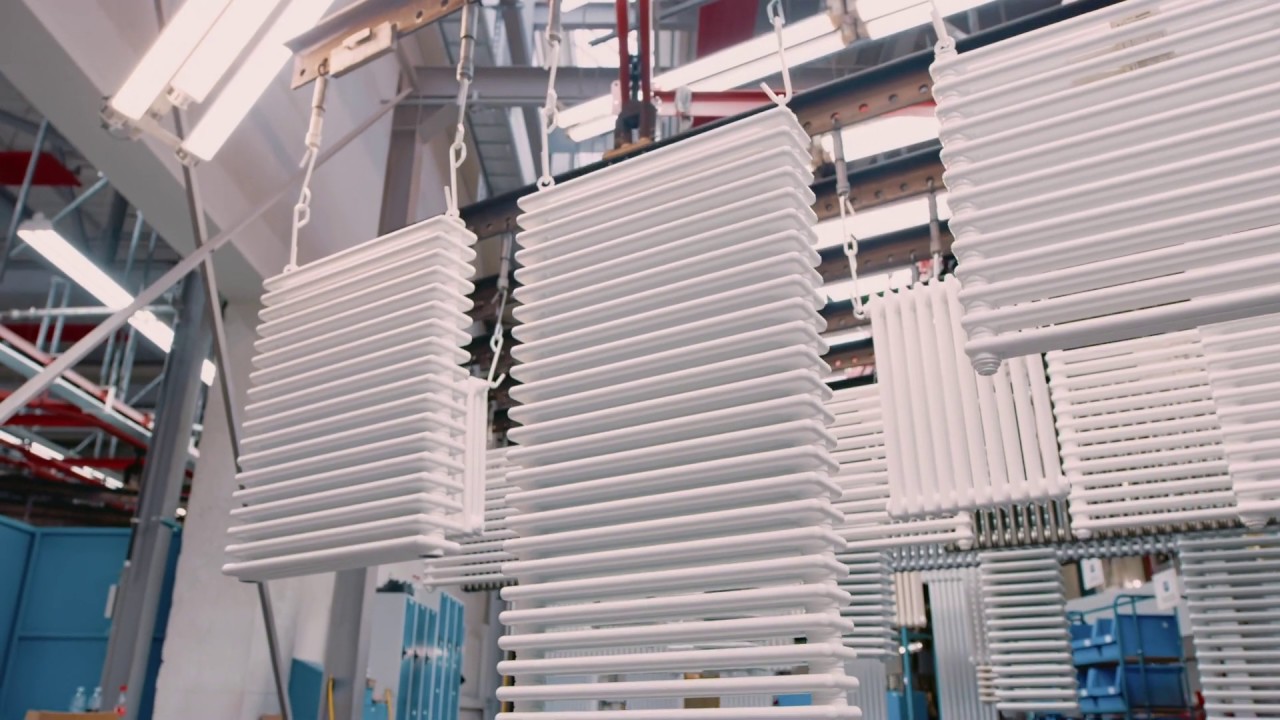
With particular emphasis on the aspects of colour, gloss and structure
Colour
By manufacturing different coating systems in one location, we are able to make use of the same colour pigments during the production of different coatings. This guarantees optimum colour matching – even under different lighting conditions.
Gloss
The coating formulation as well as the way the coating is processed are both important in achieving a desired level of gloss. The baking parameters for powder coatings and strict adherence to the mixing ratios for 2C coatings are further examples of factors influencing the level of gloss. These parameters can be identified by our application technology department and then made available to the user of the coating system.
Structure
Regardless of whether the requirement is for a smooth surface or a certain kind of surface texture – by matching different types of coating, a powder coating is often the starting point for defining a specific surface structure. In addition to the coating formulation, it is primarily the observance of the coating thickness window that ensures the correct flow properties and structures are achieved when the powder coating is baked in the oven. When using wet coatings, in particular structure coatings, that structure is then carefully matched to the template by means of optimised application parameters such as nozzle size, material pressures or application speed.
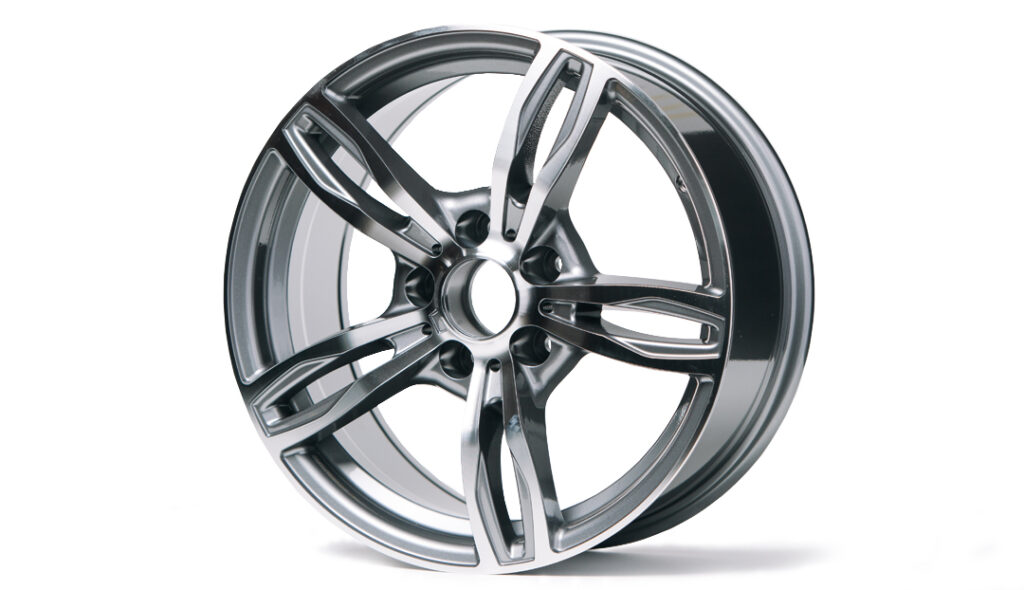
Light metal
1 of 4Base coat (Powder coating)
2 of 4Base coat (Industrial coating)
3 of 4Top coat / varnish (Industrial or powder coating)
4 of 4